Insulation Perth keeps your home comfortable and saves energy. It prevents the flow of heat from hotter areas to colder ones, stopping convection and reducing radiation.
It can be bulk or reflective insulation, depending on your climate and other factors. Bulk insulation slows heat loss by blocking air gaps, voids and building elements like framing
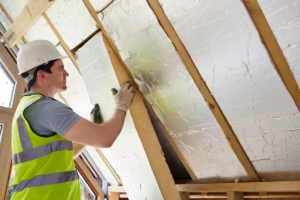
One of the most common types of insulation is fiberglass, which is made up of flexible glass fibers. The material is primarily used in walls, attics and basements in homes and commercial buildings. It’s also an excellent option for insulating pipes, heating and cooling equipment, ducts and other electrical components.
When used properly, fiberglass can provide a high R-Value, the revered measurement of an insulation’s ability to resist heat flow. However, R-Value is only part of the story when choosing the right insulation. The climatic conditions of your region and the specifics of your home’s construction can influence what R-Value you need to achieve the highest level of insulating protection.
The manufacturing process for fiberglass insulation starts with the careful selection of natural and manufactured ingredients. The main raw materials include silica sand, limestone and soda ash along with other minor components like calcined alumina, borax, feldspar, nepheline syenite, magnesite and kaolin clay [1].
Once the ingredients are combined, they’re drawn into a thin sheet using a draw furnace. This carefully regulated device maintains consistent heat and pressure to facilitate the drawing of the glass preform into a neck-down profile with remarkable speed and accuracy.
This thin layer of glass fibers entraps a great deal of gas, which provides the thermal insulation value that makes fiberglass so useful. Various binding agents and additives are then incorporated to improve the performance of the insulation and make it safe for building use. Most notably, fire retardants are added to reduce the potential risk of fire and smoke inhalation.
In addition to its thermal insulating properties, fiberglass is a good sound absorber. It can diminish the obnoxious noises produced by your HVAC system and reduce outside sounds from entering the house. It also discourages insect and rodent infestations because the material is rot-resistant and biologically inert.
For homeowners considering DIY insulation projects, there are two primary forms of fiberglass insulation available: blankets and batts. Blankets are large rolled-up sheets that are held together by reflective aluminum foil or paper acting as an adhesive vapor barrier. They’re ideal for attics that are free of obstructions and can be installed quickly and easily. The disadvantage of this type of insulation is that it can leave behind a loose dust that can irritate the lungs and skin. The material is also not entirely flameproof, so it can smolder and emit toxic gases into the air that can be dangerous to your health.
Mineral Wool
Mineral wool is an effective insulation material for walls and roofs. It keeps out the heat and cold, keeping your client’s home at an ideal temperature for their health and comfort. This type of insulation also offers significant sound-absorbing properties. Your client won’t have to worry about hearing their neighbors or their children.
Unlike fiberglass, mineral wool insulation has excellent fire-retardant properties. It’s a naturally incombustible material that doesn’t require the addition of fire retardant chemicals to the manufacturing process. It’s not only a green product, but it’s also very durable and maintains 90% of its insulating value for the life of the building. It’s also a safe material for sheathing building supports and girders, and it can be used to create fire-resistant doors and partition walls.
Like fiberglass, mineral wool is manufactured using a combination of natural raw materials and recycled sources. The natural raw materials are melted in order to be spun into fibers and then bound together with different resins and oils. The result is a soft, yet dense insulation material that can be produced in either batts or boards. It has a higher classification temperature than fiberglass, meaning that it can be used in more severe applications.
The thermal resistance of mineral wool is comparable to foam, but it has the advantage of being able to fit into tight spaces without losing its insulating value. It is also easy to cut, making it easier to install around electrical boxes and outlets, as well as into areas where ductwork will be installed in the floor. It is also very durable, withstanding the effects of abrasion and impact.
The acoustic properties of mineral wool are also outstanding. It’s a rock-based insulation, so it’s very good at blocking and minimizing the transmission of sound. This makes it perfect for apartments, schools and other public buildings where noise levels are a concern. It is also effective at absorbing sound waves, especially in the middle and high frequencies. This makes it a great choice for concert halls, where it is often used to help minimize the sound of the music and reduce the number of decibels in the auditorium.
Cellulose
Cellulose insulation is made of recycled newspaper and other paper products that are treated with a fire-retardant chemical. It can be installed in wall cavities and attics either dry or wet. When wet, it can be either blown-in loose-fill or spray-applied damp. It can also be dense packed or available in batts. It is a flexible material that is able to conform around obstructions in walls such as wiring and ducts. It is often used in retrofitting older homes, but it can be applied to new construction as well.
Historically, it was often installed as dry blown insulation in new and existing home construction. This involved drilling a series of three-inch holes in the sheathing and using a special blower machine to fill wall cavities and attics. However, this method of installation often resulted in wide gaps between the studs. This could result in the insulation losing some of its effectiveness. Modern cellulose insulation can be dense-packed to minimize these problems.
In general, cellulose can be expected to perform better than fiberglass in terms of reducing energy costs. Its density allows it to fill small gaps and crevices that would otherwise allow air leakage, reducing the amount of energy needed to heat or cool the building. This can result in significant savings for the homeowner over time.
It is important to note that the insulating value of cellulose can decrease over time as it absorbs water and breaks down. It is therefore important that the product be kept dry, which can be done by sealing air leaks in the building envelope with caulking and weather stripping.
Some studies have shown that cellulose can offer better fire resistance than fiberglass as it limits the oxygen flow in the event of a fire, thereby slowing down the spread of flames. However, this benefit is only relevant when the product has been properly manufactured and installed. Greenfiber meets or exceeds the safety standards of the Consumer Products Safety Commission (CPSC) for fire testing and carries a full Underwriters Laboratories label.
While mold growth on cellulose can occur, it is usually the result of a moisture problem in the building envelope such as a burst pipe or roof leaks. It is important to note that the cellulose itself is not susceptible to mold growth, only the wood materials it has been bonded to.
Spray Foam
Spray foam insulation consists of unique liquid components that react on site to expand into an insulating, air and moisture barrier. It is a very effective and versatile material for insulating a home or building. It can seal wall cavities, attics, crawl spaces, ceilings, exterior walls, and small gaps and cracks in a home. It is an energy efficient option to reduce heating and cooling costs by limiting air infiltration and movement throughout the house.
It is also an excellent specialty packing material that protects sculptures, vases, large fossils, lamp bases, busts and many other items of unusual shape from damage during transport. This is due to the fact that spray foam expands up to 30-60 times its original liquid state when sprayed onto a surface, uniformly cushioning the object while conforming to it’s shape.
Closed-cell and open-cell spray polyurethane foam (SPF) differ based on their makeup of tiny air bubbles within the cured foam. Closed-cell is much harder and more rigid and typically has a higher R-value per inch than open-cell foam. Its cellular structure provides a tight air barrier, which improves efficiency and comfort by limiting unwanted heat transfer through a building envelope.
The R-value of closed-cell spray foam is determined by how much the blowing agent expands the foam cells, as well as by the chemical mix used in the formulation. Most manufacturers use hydrofluorocarbons as the blowing agents in their products because they have a lower global warming potential than carbon dioxide, on a per kilo basis.
In addition to limiting the amount of IR radiation emitted by the substrate it can also limit vapor movement and reduce condensation, which is especially important in humid areas. This makes it an excellent choice for homes in climates with extreme weather variations.
It is very durable and can withstand heavy objects being dropped on it, as well as moisture and abrasion. It adheres well to most construction materials, assuming the substrate is clean, dry and free of oils, greases and dirt. It may not adhere to certain plastic sheeting, under-cured concrete or some metals, but these limitations can usually be overcome with a primer or coating before the spray foam is applied.